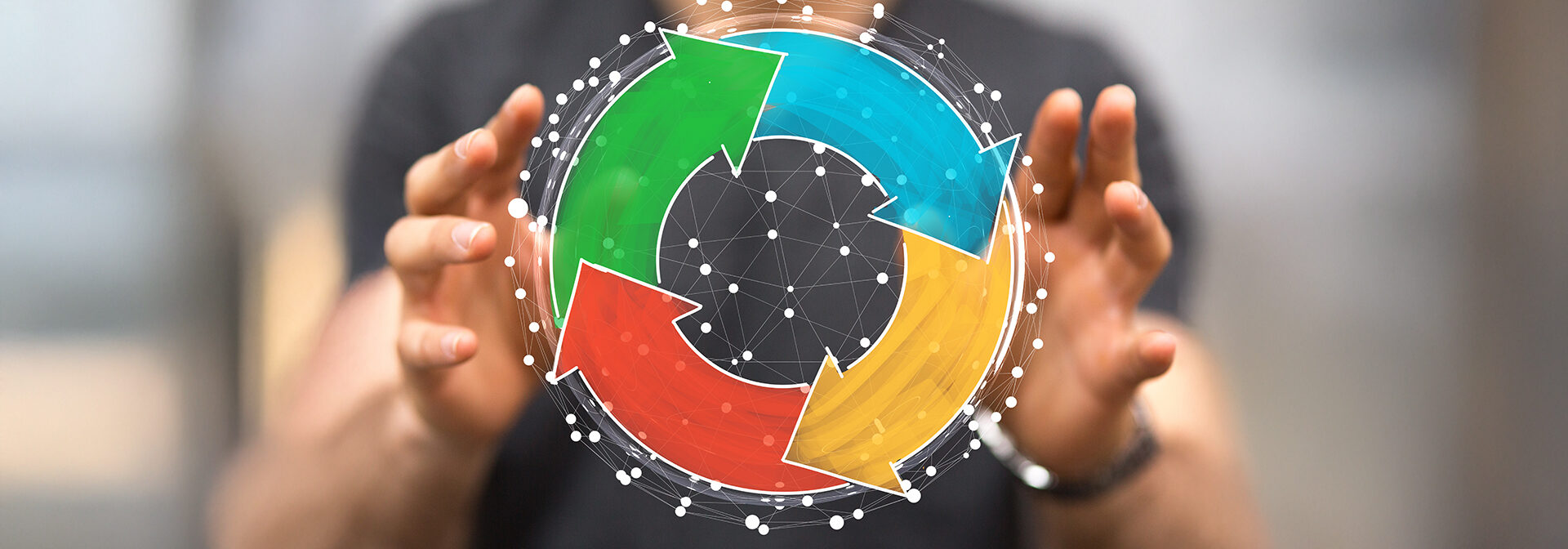
Continuous improvement enables reliability growth
Have you ever come across an acronym called FRACAS? While many might recognize its components—Failure Reporting, Analysis, and Corrective Action System—its true potential goes far beyond the letters. When implemented effectively, FRACAS can transform an organization by turning failures into powerful opportunities for continuous improvement. But how can this system be embedded seamlessly into everyday processes, driving tangible results and operational excellence?
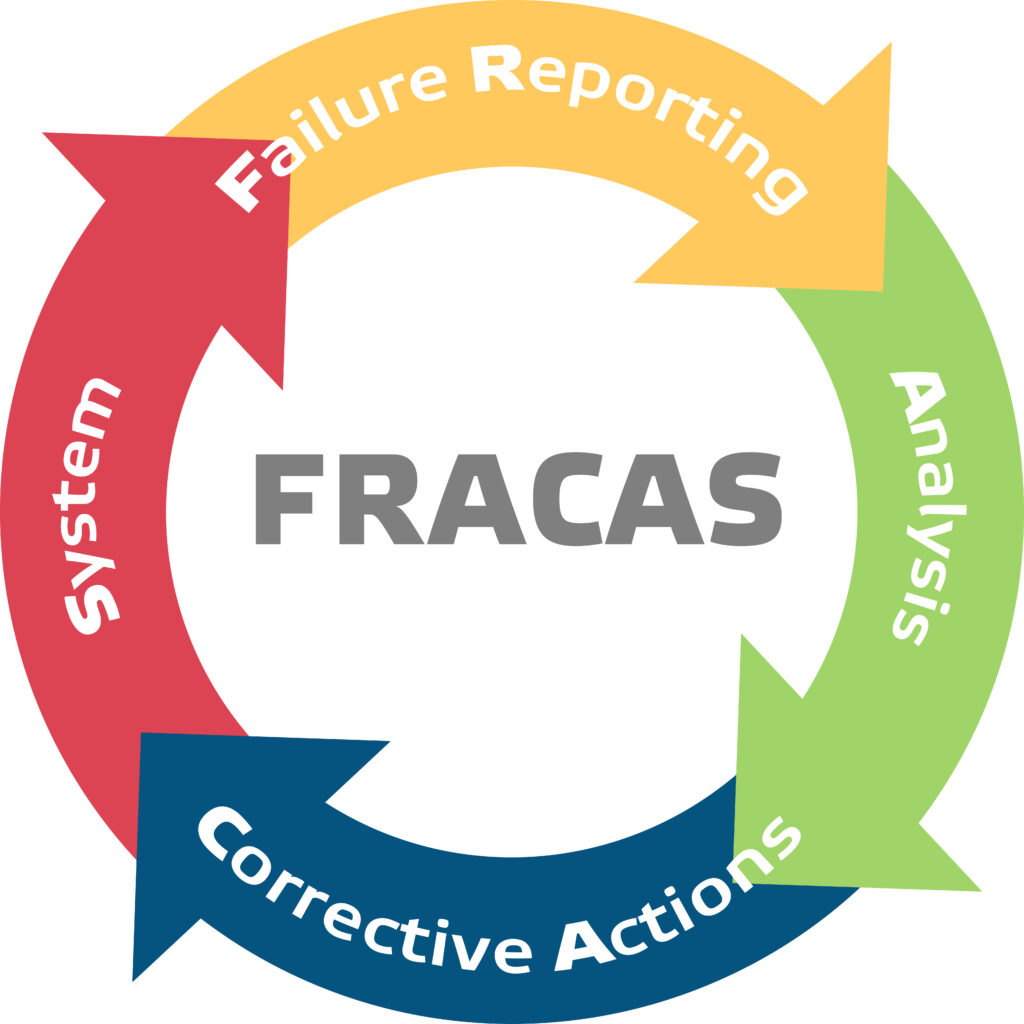
Failure reporting and analysis is essential to achieving and sustaining a product’s reliability and maintainability. Once the data is analysed, it is important to identify the necessary corrective actions and determine how to implement them effectively. Since FRACAS should be a continuous loop rather than a one-time exercise, the data should be revisited after the corrective actions are made to confirm their success and ensure lasting results.
There are plenty of benefits that operating the FRACAS loop can bring to the organization, including direct savings in warranty costs, as well as reduced penalties, rework, and material waste. Indirect savings arise from enhanced customer satisfaction, improved insight into product portfolio performance, and the development of preventive maintenance strategies. Furthermore, FRACAS provides valuable lessons learned for next-generation product development, ensures effective control of preventive and corrective actions, and deepens understanding of the operating environment of the installed base. The railway quality management system standard ISO 22163 (IRIS) also mandates the use of a FRACAS or similar system to detect and analyse the performance of the products in operational use.
The most significant advantage of operating the FRACAS loop lies in the lessons learned. Leveraging data from the installed base is invaluable, as the best information available comes from the actual use conditions. By analysing field data and customer feedback, FRACAS enables designers to consider real-world usage scenarios and improve the product’s robustness in those contexts.
Teleste operates a dynamic FRACAS loop for its Public Safety and Mobility product portfolio. Field failure, testing, and production data are consolidated and reviewed monthly, with key findings reported to the business management quarterly. All the FRACAS data is available for various internal teams, and more detailed analyses are encouraged to different needs.
Incorporating FRACAS into the product development lifecycle enables us to create more reliable, efficient, and user-friendly products. By capturing and analysing failure data, prioritizing issues based on their impact, and fostering continuous improvements, FRACAS helps us identify design weaknesses early. This proactive approach reduces the likelihood of future failures and helps us ultimately build products that are safer, more durable, and more successful in the market.
Kati Kokko
Kati Kokko
I am RAM and LCC specialist at Teleste’s Rolling Stock Manufacturers / Rail Information Solutions organization. I joined Teleste in May 2020, and I have wide experience in electronics reliability and electronics industry. I have experience in research at university as well as leading reliability team in electronics industry. I hold a Doctor of Technology degree in electronics. You can find more about me in my LinkedIn profile.
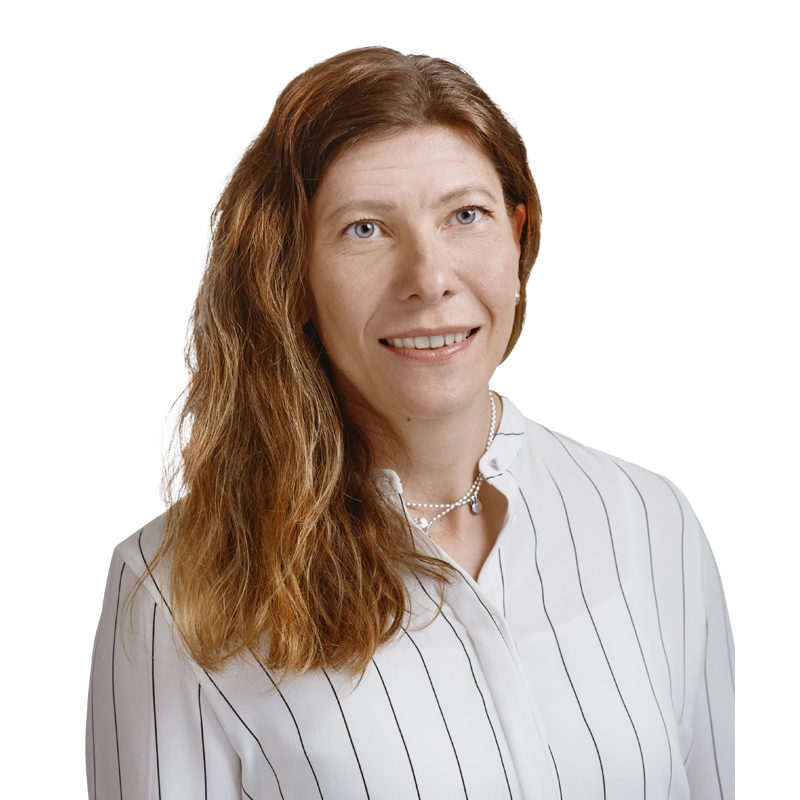