
Smart broadband amplifiers call in for smart manufacturing
One of the broadband industry news this year has been the new standard released by the Society of Cable Telecommunications Engineers (SCTE), which defines a single information model for broadband amplifiers used in DOCSIS 4.0 networks. The standard provides a layer of communication capability on the cable network, enhancing the usage of automation and electrical controls in the amplifiers, that are to turn them smart.
While the addition of the communications element to amplifiers is very welcomed in terms of increasing operational efficiencies, it will have profound effect on the way the amplifiers are made. Throughout the DOCSIS generations, technology vendors have utilised manufacturing methods that have traditionally produced good quality amplifiers capable to meet operators’ needs in the field. However, in the realm of smart amplifiers, these traditional methods are no longer valid as such; instead, a new approach to manufacturing is needed to reach the level of precision and fine-tuning required by the devices.
Since the inception of our Intelligent Networks concept more than 10 years ago, the integration of automation and intelligence in HFC actives has been a longstanding practice at Teleste. In fact, our first intelligent amplifier was deployed in the field as early as 2008. Over the years, the technology has evolved from its initial stages to become a comprehensive and extensively adopted portfolio. Through the collaboration with major operators, we have also accumulated a wealth of hands-on experience, refining how automated features, like self-alignment, perform under less-than-ideal field conditions.
The key learning from our journey can be summarised as follows: the smart amplifiers only work in the field exactly as specified when manufactured absolutely correctly. The more accurately the devices are set and calibrated during the manufacturing process, the more precisely will the smart features operate in a real network.
Achieving the required level of accuracy in amplifier manufacturing necessitates a seamless match between the smart amplifier and its production environment right from the start. Our smart manufacturing approach encompasses a range of factors and considerations during the design phase, ensuring optimal performance, quality, and manufacturability of the amplifiers while proactively addressing potential issues.
We have revolutionized the manufacturing process by replacing many traditionally manual steps. For example, parameters for gain calibration are set using software and automated tuning and testing procedures have also been implemented. Our smart amplifiers also possess the capability to be controlled and commanded using our dedicated test software, while also having the ability to conduct self-testing and measurement of certain functions. All in all, previously manual process steps are handled automatically today.
The usage of automation and software allows for more uniform and comprehensive parameter adjustment compared to manual methods, significantly enhancing precision and efficiency, and minimising the risk of human error. In addition, the measurement of multiple parameters is enabled with superior consistency and accuracy. This facilitates easier monitoring of production yield and error detection, as the measurement results are meticulously tabulated to generate valuable data for troubleshooting and analysis.
By integrating software, automation, and smart amplifier design into our smart manufacturing processes, we ensure precise control, in-depth measurement capabilities, and heightened error detection. The outcome is a smart manufacturing environment that empowers us to deliver top-notch devices that operate in strict accordance with their designated specifications. This strategic alignment ensures that we maximize the value and performance of our amplifiers, enabling our customers to fully reap the operational benefits provided by the smart features and functionalities.
Toni Rumpunen
Toni Rumpunen
Passionate R&D professional interested widely in technology and people. Responsible of HW development at Teleste for over a decade with HW designer background. Building cross functional collaboration and drilling holes between organizational silos. See my LinkedIn.
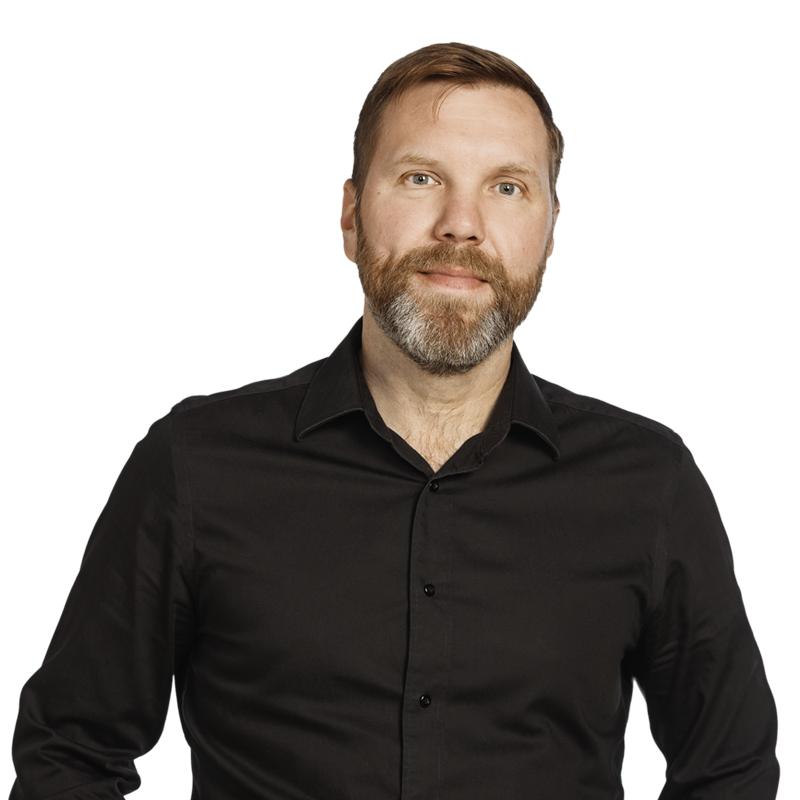