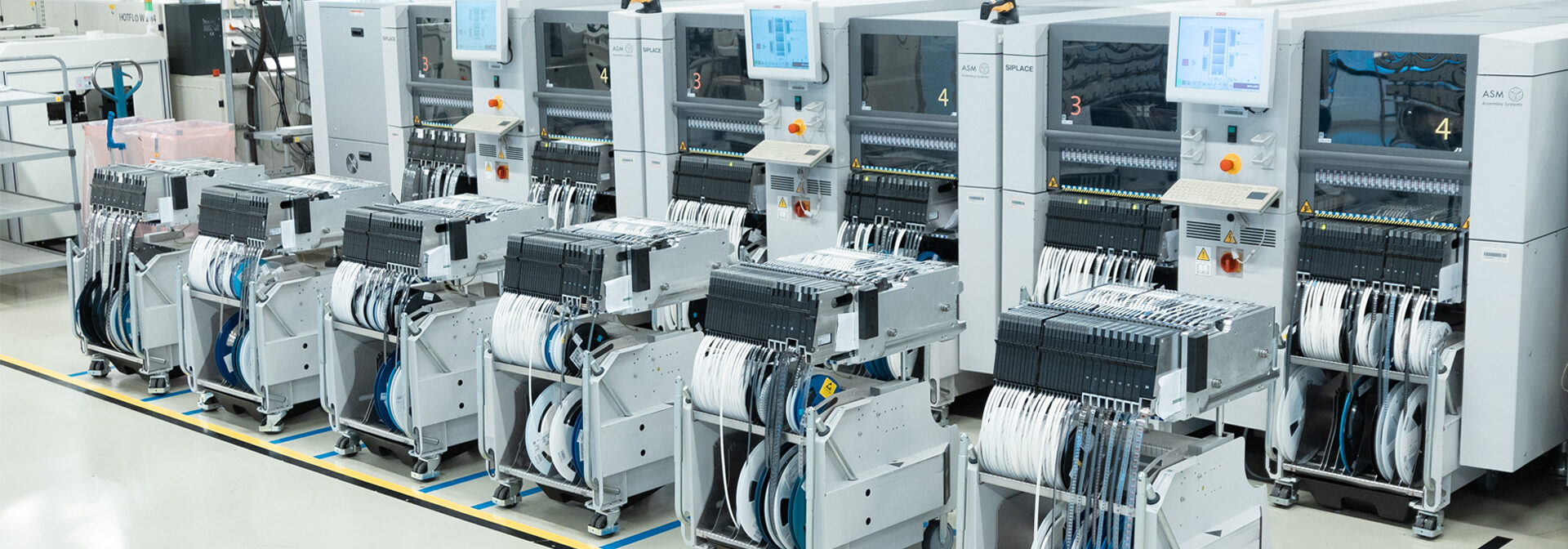
Mastering Capacity and Scalability: The Key to Future-Ready Manufacturing
In early 2024, Teleste became the first technology vendor to deploy 1.8 GHz smart amplifiers in live broadband networks across North America. This milestone demonstrated not only our technical expertise but also the strength of our manufacturing capabilities. Our proactive and scalable production strategy allows us to successfully transition to volume manufacturing of these high-performance products, while ensuring our capabilities to serve customers on other markets.
Capacity optimization: A strategic imperative
To thrive in today’s competitive market, manufacturers must ensure they can meet increasing customer demands while staying agile and efficient. A well-structured approach to capacity and scalability enables businesses to anticipate market shifts, align production capabilities, and maintain flexibility even in unpredictable conditions.
A structured approach to capacity management starts with a deep understanding of production capabilities at every level. At Teleste we have identified four key pillars that help us maintain efficiency, agility, and long-term growth:
- Data-driven decision-making
- Agile production cell concept
- Smart tools and automation
- Skilled workforce and collaboration
Leveraging these foundational elements allows us to effectively utilize our resources, improve forecasting accuracy, and streamline and scale operations to better meet customer expectations.
Leveraging data for seamless operations
Accurate forecasting and planning form the backbone of effective capacity management. By utilizing rolling 18-month sales forecasts, we continuously monitor production needs at both weekly and daily levels. This approach allows for precise resource allocation and rapid scalability when demand fluctuates.
Incorporating real-time data analytics helps manufacturers identify potential bottlenecks before they impact operations. By proactively managing supply chains and assessing component and resource availability, disruptions can be prevented and smooth production flow maintained. A data-driven strategy also minimizes operational “waste”, ensuring efficient allocation of resources and rapid scaling when needed.
Implementing agile cells for maximum efficiency
Manufacturers must build workflows that balance efficiency with flexibility. At Teleste, the core in achieving this are our agile production cells, which enable rapid transitions between product orders and lines. These cells are designed to adapt quickly, allowing seamless changes from one order to another within the same product line in just 30 seconds, and between different product lines within 30 minutes.
Beyond in-house production, our cells are designed for mobility. They can be deployed to contract manufacturing partners within 24 hours using just an internet connection and electricity, significantly reducing lead times and increasing localized manufacturing capabilities.
Additionally, we optimize product throughput times with a two-phase “configure-to-order” approach. By preparing base-configured products in advance and customizing them during final assembly, we reduce production time while maintaining the flexibility to cater to customer-specific requirements at scale.
Smart Manufacturing: Enhancing efficiency and quality
Integrating smart manufacturing techniques helps streamline production workflows and improve quality control. For instance, intelligent picking systems minimize component retrieval times and reduce human picking errors, while a unique feature of our production, the automated testing and tuning of our intelligent network devices, ensures their precision and compliance to specifications and customer requirements. Significantly contributing to product quality, these automated production phases also add efficiencies by freeing our personnel for other production phases.
Skilled workforce and strategic collaboration
While automation and smart tools enhance are increasingly widely utilized, a skilled workforce remains an essential component of scalable manufacturing. Teleste’s flexible staffing model integrates in-house teams with an adaptable workforce that helps us accommodate changes in demand levels. These include a network of skilled students at our Littoinen factory, who can seamlessly integrate into our production process during peak demand periods. Collaboration with electronics contract manufacturers further expands capacity while allowing us to maintain strict quality and delivery standards.
Close collaboration between our production and R&D teams enhances agility, enabling a 24-hour turnaround for R&D prototype orders and seamless transition from design to production within days. This streamlined approach shortens development cycles, speeds up product launches, and facilitates rapid troubleshooting—driving innovation and continuous improvement.
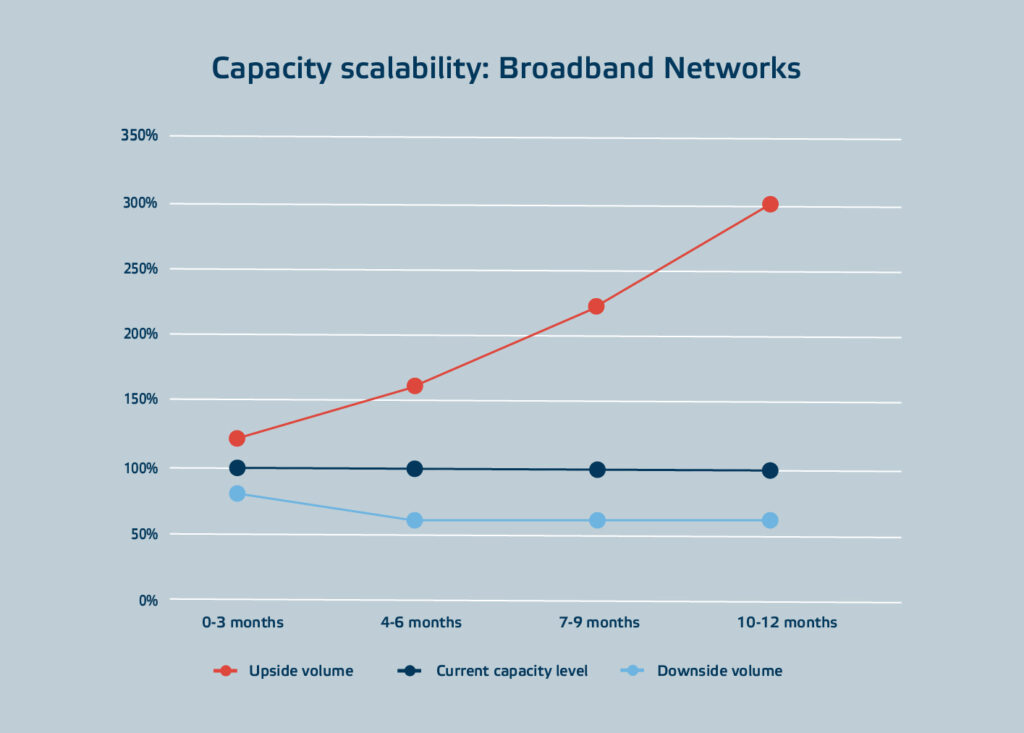
The future of manufacturing: Adapting to stay ahead
For forward-thinking manufacturers, controlling production capacity is not a challenge but driver of success. Incorporating smart manufacturing, predictive analytics, and scalable production solutions, businesses can shift from merely reacting to market changes to actively driving innovation. The future belongs to manufacturers who can scale intelligently, adapt seamlessly, and innovate continuously.
Are you ready to take your manufacturing strategy to the next level? By embracing these key principles, you can enhance efficiency, ensure scalability, and position your business for sustained success in the evolving industrial landscape.
Turkka Lehtonen
Turkka Lehtonen
I’m Operational Director at Teleste’s manufacturing facility in Littoinen, Finland. See my LinkedIn.
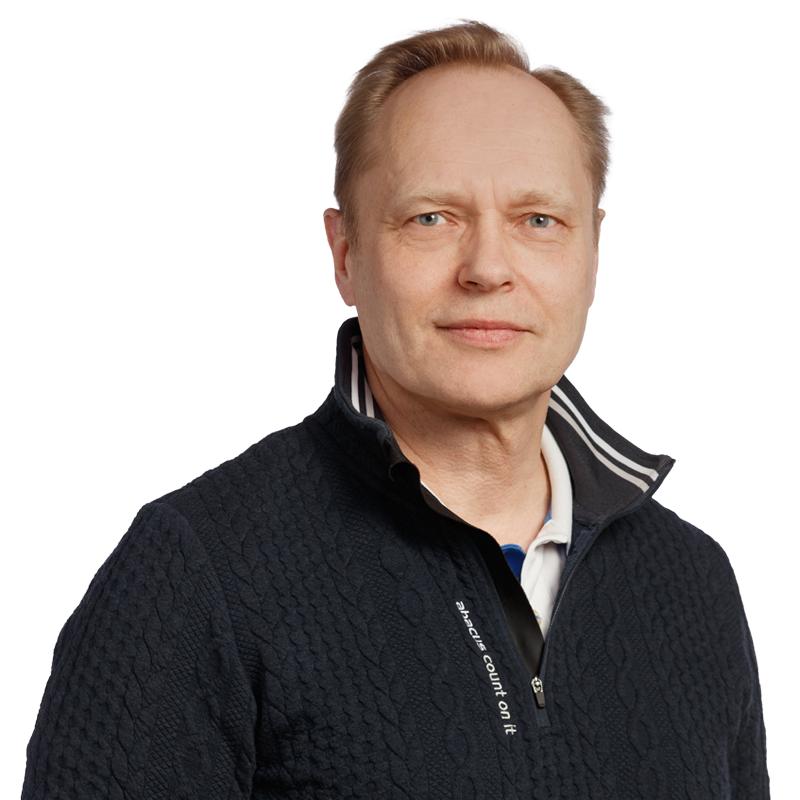